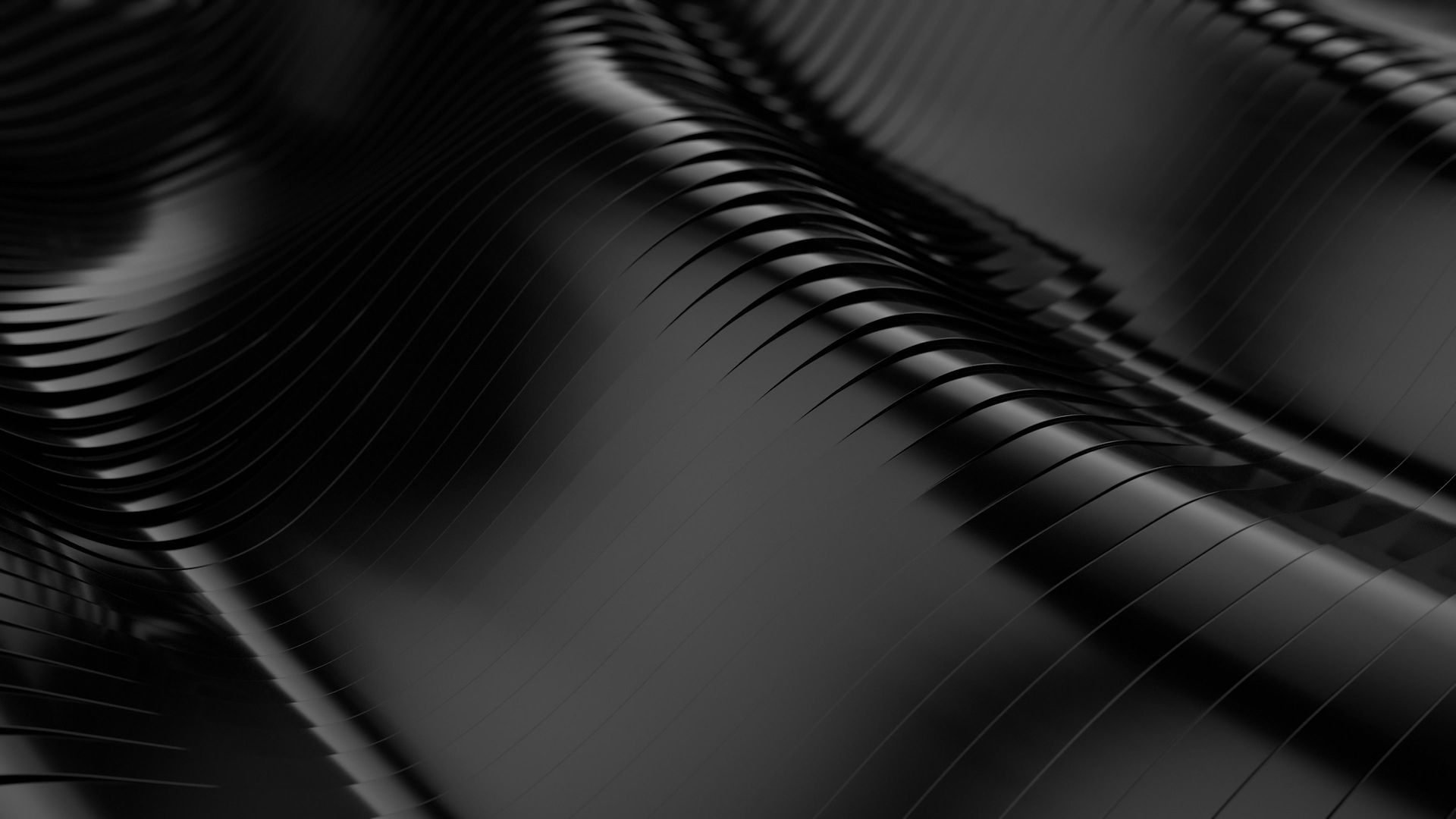
Work Flow
This project consisted of two parts. The first consisted of a single assembly lab and the second the entire manufacturing plant. The results (depicted below) are for the conclusions used to optimize the single lab, however, the methodology was expanded and applied to all assembly operations.
The first project in this topic was to optimize an assembly lab. This lab was unique to the company, consisting entirely to assemble and test a single unit.
Although, we had the access to modify tooling move work stations, and assign labor responsibilities we were unable to change part configurations or the assembly operations.
We were able to design or buy new tooling, as well as reconfigure the workstations. While these efforts aided the operators the real insight into improvement came after conducting a time study and workflow diagram (spaghetti diagram). This showed critical time loss from the operational structure (Operators waiting for the next task to be completed before proceeding) and unnecessary part touches/movements.
After reordering operations based on setup/run time and functionality we transformed the cell as follows...